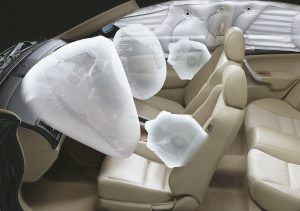
HAVA YASTIĞI
İlk kez 1970’li yılların başında kullanıma başlayan hava yastığının son 5 yılda kullanımı yaygın hale gelmiştir. 1 eylül 1998 tarihinden itibaren federal güvenlik standardı Amerika Birleşik Devletlerinde satılan arabalarda hem yolcu hem de sürücü hava yastığını zorunlu hale getirmiştir. Hava yastığı bir tetikleme mekanizması ile çalışmaktadır. Bu mekanizma kimyasal maddeleri harekete geçirmektedir. Hava yastığı, 48km/h üstünde hızı olan bir arabanın önden ya da yandan çarpışması sonucu devreye girer. Hava yastığı 40 milisaniyeden daha kısa sürede şişecek şekilde tasarlanmıştır. 0.03 saniye ile 0.06 saniyede tam anlamıyla şişmiş olur. Balonu şişirecek kimyasal mekanizma 40-54 milisaniye de aktif hale gelmektedir. Panel içinde yerleşen balon saatte 322 km/h hızla fırlayarak nitrojen gazı ile şişmeye başlar. Bu hızlı patlama sonucunda sürücü ve yolcuda çeşitli yaralanmalar olabilmektedir. 10 yaşın altındaki çocuklarda eğer arabada hava yastığı var ise ölüm oranı % 21 gibi yüksek bir değerdedir. Hava yastığı kumaşı sıcak gazlara karşı dirençli yapıda olmalı ve yüzeyinde erime olmamalıdır. İleriye hareketli ilk yapılan hava yastığı Neopren kaplı (Dupont) kaplı nylon6.6 kumaşındandı.
Sonraları silikon kaplanmışlar ortaya çıktı. Günümüzde hava yastıklarında 210-840dtex aralığında Avrupa ve Japonya’da 470dtex numarasında nylon6.6 yüksek mukavemetli filament esaslı bezayağı bağlantılı dokuma kumaşlar kullanılır. Nylon6 lifleri de tercih edilmektedir. Nylon 6 daha yumuşak olduğundan deri sürtünmesini azaltır. Kaplanmamış kumaş yaklaşık 170-220 g/m2’dir. Avrupa’da sürücü tarafındaki hava yastıkları yaklaşık 40-65 litre kapasitelidir. Ön yolcu hava yastıkları biraz daha büyüktür. Amerika’da kullanılan hava yastıkları Avrupa’da kullanılandan daha büyüktür. Avrupa’da hava yastıkları emniyet kemeri ile birlikte tasarlanmaktadır. Hava yastığı için gerekli olan kumaş miktarı hava yastığının araba içindeki bulunduğu yere göre değişmektedir.
Hava yastığı üretiminde ilk olarak 840denye nylon6.6 poliamid tür iplik kullanılmakta idi. Nylon6.6 çok üstün mukavemet, enerji yutum, ısıl direnç, sertlik özellikleriyle tercih edilmektedir. Nylon6.6 ile karşılaştırıldığında, poliester esaslı bir kumaşı eritmek için %30 daha az enerji gereklidir. Poliesterden yapılan bir hava yastığı patlayıcı kimyasallara
karşı daha dayanıksızdır. Nylon6.6 lifinin diğer bir avantajı düşük özgül ağırlığıdır. Aynı çapta iplikten dokunan kumaşlardan poliester, nylon6.6’dan %20 daha ağırdır. Nylon6.6 ayrıca sert iklim şartları altında uzun süre özelliğini kaybetmemesiyle bilinmektedir. Bu kumaş üzeri neopren kaplıydı. Günümüzde ise nylon6.6 iplikten dokunmuş üzeri silikon kaplı kumaş kullanılmaktadır. Daha ucuz olan ve bulunması kolay neopren kaplaması yerine silikon kaplaması, güç tutuşma özelliğinin daha iyi olması, aşınma direnci, esneklik, düşük gaz geçirgenliği, ısı ile eskimeye dirençli ve düşük sertlik özellikleriyle daha çok tercih edilmektedir.
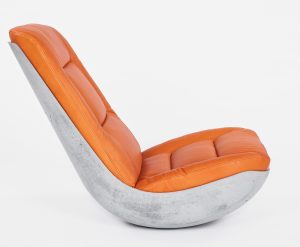
KOLTUKLAR
Araba koltuklarının içerisinde döşemelik kumaş, poliüretan köpük ve astar kumaşı bulunmaktadır. Araç üreticileri üst tabakası dokuma, orta tabakası poliüretan köpük ve alt tabakası poliamid çözgülü örmeden oluşan 3 tabakalı kompozit yapıyı, performans ve maliyet olarak başarılı bulmuştur. Köpüğün amacı kumaşın torbalaşmasını ve buruşmasını engellemektir. Astar kumaş, nylon veya polyester lifinden çözgülü örme tekniği ile üretilir. Astar kumaşı, döşemelik kumaş ve süngerin birlikte koltuk iskeletine giydirme sırasında yardımcı olur. Araç içerisindeki tekstil materyal maliyetinin yaklaşık %30-40’ını döşemelik kumaşlar oluşturmaktadır.
Döşemelik kumaşlarda eskiden nylon kullanılıyorken günümüzde poliester en çok kullanılan lif konumundadır. Aşınmaya karşı direnç, UV ışığa direnç, kolay temizlenebilirlik, küflenmeye karşı direnç ve iyi derecede yırtılma mukavemeti gibi özellikler, poliesterin kullanımını artırmıştır. Nem almaması ve nem transferi yapmaması olumsuz özellikleridir. Döşemelik kumaşlarda yün ipliği doğal güç tutuşur olması (LOI25) ve iyi derecede nem alma özellikleriyle poliester ile birlikte üst sınıf araçlarda karışım yapılarak kullanılmaktadır. Araba koltuklarında kullanılacak liflerde başlıca olarak UV ve sürtünmeye dayanımı özelliği aranmaktadır. 1960’lı yıllarda tercih edilen PVC’nın yerini 1970’li yılların başında nylon6, nylon66, akrilik, yün, polyester lifleri kullanılmıştır. Nylon6 lifi özellikle gün ışığı bozunmasına uğrar. Akrilik lifinin ise sürtünmeye dayanımı sınırlıdır. Yün pahalıdır. Performans/maliyet oranı uygun lifler tercih edilmektedir. Bu alanda en çok poliester lif kullanılmaktadır. Polipropilen lifi sürtünmeye karşı direnci çok iyidir ancak güneş ışığına dayanımı kötüdür. Bu kumaşlar genellikle filament tekstüre polyesterden imal edilmektedir.
Kesikli liflerden yapılan ipliklerin sürtünme direncinin az olması nedeniyle daha az tercih edilir. Dokuma için 167 dtex/48 filament dörde beşe katlanıp kullanılır.
Dokuma Kumaşlar – 200-400 g/m2
Kadife dokuma kumaşlar – 360-450 g/m2
Raşel örme kumaşlar – 280-370 g/m2
Çift iğne barlı raşel makineleri tarafından üretilen kadife örme kumaşlar dokuma kadife kumaşlara kıyasla daha çok tercih edilmektedir. Çift iğne barı arasında kadife kumaş oluşturulmaktadır. Sonrasında kesilmektedir. Örme kadife kumaşlar daha dökümlüdür ve havları dökülmeye karşı daha sağlamdır. Dokuma kadife kumaşlarının havlarının dökülmemesi için kumaşın arkasına kimyasal kaplama yapılmaktadır.
Araba koltuklarında kullanılan sünger ısı ve ışığın etkisiyle döşemelik kumaşın sararmasına yol açabildiğinden, sünger yerine monofilamentlerle bağlanmış çift plakalı raşel kumaş veya dokunmamış kumaş endüstrisinde tülbendin dikine katlanmasıyla üretilen sıkıştırıldıktan sonra tekrar eski haline gelme özelliğine sahip “STRUTO” materyali kullanılabilmektedir. Süngerin maliyetinin düşük olması tercih edilme nedenidir.
Döşemelik kumaş türleri incelendiğinde, Avrupa Bölgesinde düz dokuma kumaşın, Amerika Bölgesinde kadife kumaşın ve Asya Bölgesi ise trikot örme kumaşın en çok kullanıldığı çok açık görülmektedir. Döşemelik kumaş türlerinde Asya Bölgesinde triko kumaşın, Avrupa bölgesinde düz dokuma kumaşın, Amerika Bölgesinde ise dokuma kadife kumaşın en fazla tercih edildiği vurgulanmıştır. Yeni nesil araçlarda örneğin Mazda tarafından üretilen aracın döşemelik kumaşı, şeker kamışından elde edilen polilaktik asitten üretilen filament esaslı iplikten dokunmuştur. BMW tarafından geliştirilen Gino isimli aracın dış kaportası kumaştan yapılmıştır. Bu araçta elektro hidrolik tellerden destek alarak açılır kapanılır özellikteki ön kaput bulunmaktadır.
HALILAR
Halılar konfor özelliklerine ilaveten titreşim sönümleme, ısı yalıtım ve ses yutum özellikleriyle ulaştırma araçlarının içerisinde kullanılmaktadır. Genellikle halılarda iğneleme teknolojisiyle üretilmiş dokunmamış kumaşlar paspaslarda tafting (dokuma kumaşın dikilerek ilmekli yüzey oluşturma) yöntemiyle üretilmiş materyaller tercih edilmektedir. Binek araçta yaklaşık olarak3.5-4.5m2 kumaş kullanılmaktadır.
Ulaştırma alanında halı ve paspas üretiminde başlıca olarak kesikli polipropilen, polyester ve akrilik lifleri kullanılmaktadır. Bu liflerin çoğunluğu tekstil ve hazır giyim fabrikalarından toplanan kumaş atıklarının tekrardan
lif haline getirilmesiyle elde edilmektedir. Üretim teknolojisi olarak tülbent esaslı kumaş teknolojisi (nonwoven) kullanılmaktadır. Bu alanda kullanılan kumaşların birim metre kare ağırlığı 500 ile 2000g/m2 arasındadır. Paspas üretiminde tafting teknolojisi ile üretilen kumaşlar maliyeti sebebiyle çok az talep edilmektedir. Yer halısı, bagaj halısı ve paspaslar bu sınıfta yer almaktadır. Arabaların içerisinde çok fazla zaman geçirildiğinden yemek yendiğinden antibakteriyel gümüş içeren kesikli lifler, halı üretiminde harman içerisine %1-5 oranında karıştırılabilir.
Tarak makinesi, dokunmamış kumaş endüstrisinde, kesikli liflerden tülbent doku oluşturan makinedir. Başlıca olarak brizör, çalışıcı, alıcı, tambur ve penyör silindirlerinden oluşan bu makinede genellikle 30mm ve üzeri kesikli uzunluğa sahip rejenere ve sentetik liflerden tek veya çift kat şeklinde tülbent üretilmektedir.
Tercihli lif yönlendirmesiyle lifler birbirine paralel veya karışık şekilde dağıtılabilmektedir.
Çapraz serme makinesi de tarak makinesinin çıkışına konan tarak makinesinden çıkan tek veya çift kat tülbendi istenen genişlikte ve katta üst üste katlayarak ön iğneleme makinesine sevk eder. Bu makinede bulunan birçok bant ve serici silindir tülbende zarar vermeden birbiri üzerine serer. Otomotiv endüstrisinde ağır kumaşlar istendiğinden serme makinesi muhakkak üretim hattında bulunmak zorundadır.
Dokunmamış kumaş endüstrisinde kesikli liflerden hacimli tülbent üretmek istediğinde kullanılan doku oluşturma makinesi “hava ile serme”dir. Bu makinede hazır giyim işletmesinden çıkan kumaş parçalarından geri kazanılmış lifler, kâğıt ve sünger atıkları, çeşitli tüyler, kenevir, jüt, sisal gibi bitkinin gövdesinden elde edilen lifler ve cam elyafı tülbent haline getirilebilmektedir. Hava ile serilmiş tülbendin akrilik esaslı kimyasal maddelerin püskürtülmesiyle veya tülbent içerisine karıştırılan bağlayıcı liflerin fırın veya kalender silindirleriyle eritilerek bağlanmasıyla hacimli hava ile serilmiş kumaşlar üretilebilmektedir. Şayet mukavemetli kumaş üretmek istendiğinde hava ile serilmiş yapılar iğneleme teknolojisi ile de bağlanabilir. Otomotiv sektöründe araba üreticileri ekolojik olarak çevreye ve insana zararı olmayan materyalleri kullanmaktadır. Bitkisel lifler, cam, karbon gibi liflere kıyasla çevre koruma, geri dönüşüm ve düşük özgül ağırlık gibi özelliklere sahiptir. Örneğin Mercedes-Benz E sınıfı araç modellerinin kapı panellerinde bitkisel lif esaslı kompozit yapılar kullanılmıştır. Bu yapı içerisinde yer alan keten/kenevir lifleri epoksi maddesi ile kaplanmıştır.Bu sayede cam lifleri ile yapılan kapı panellerine kıyasla %20 azalma sağlanmıştır. Aynı zamanda mekanik özelliklerde geliştirilmiştir. 1999 yılında 21000 ton bitkisel lif Avrupa otomotiv endüstrisinde kullanılmıştır. Bu liflerin yaklaşık %70’, Doğu Avrupa ve Asya bölgesindeki ülkelerden ithal edilmiştir. %30’u Avrupa Birliği içerisindeki ülkelerden sağlanmıştır. Bitkisel lif esaslı kompozit yapılar kapı panellerinde, bagaj astarı olarak ve müzik sistemlerinin yer aldığı arka panelde üretiminde kullanılmaktadır.
Günümüzde endüstriyel üretim miktarının önemli oranda artmış olması dünya toplumunu kirliliği azaltmak için mücadele etmeye sevk etmiştir. Anorganik cam lifleri tülbent esaslı kumaş endüstrisindeki proseslerde diğer liflerle belirli oranlarda karıştırılmakta, kumaş haline getirilmekte ve pres makinelerinde istenilen şekilde basılarak ve otomotiv sektörüne sevk edilmektedir. Cam lifi ilavesiyle daha sert ve darbeye dirençli ve kırılmayan kompozit yapıların üretimi mümkün olmaktadır.
KOMPOZİT ÜRÜNLER
Otomotiv endüstrisinde kompozit ürünlere örnek olarak Anadol aracının dış kaportası verilebilir. Anadol, 1963 yılında ilk üretimine başlanan 1966 yılında seri üretime geçen 1980’li yılların başında üretimine son verilen dış kaportası cam elyaf ve poliester reçine olan bir araçtı. Günümüzde de cam filament ipliklerin birbiri üzerine yatırılmasıyla üretilen çok eksenli kumaşların epoksi veya poliester reçine ile RTM teknolojisiyle (birbiri içerine geçen iki kalıp içerisinde kompozit üretimi) üretilen kompozit yapılar, araçların rüzgârlık, çamurluk, tampon gibi parçaların üretiminde kullanılmaktadır. (Şekil11)
HORTUMLAR
Araçların hidrolik hortumlarında ve filtre alanında polifenilen sülfit (PPS) esaslı filamentler kullanılmaktadır. Polifenilen sülfit esaslı filamentler, 200°C sıcaklığa kadar dayanıklıdır. Doğal güç tutuşurluk özelliğine sahiptir. Üstün mekanik özelliğe sahiptir. Limit oksijen index değeri 50’dir. Karbon, aramid ve cam elyaflarıyla çok iyi lif/matris yapısında kompozit oluşturabilmektedir.
Gaz ve sıvı filtrasyon alanında, yüksek sıcaklıkta kimyasal maddelere dayanım özelliğine sahip PPS filament esaslı dokunmamış kumaşlardan yararlanılmaktadır. Yağ ve yakıt filtrasyonunda, poliester PBT kullanılmaktadır. Bu maddeden eriyikten püskürtme yöntemiyle üretilen, mikron mertebesinde liflerden oluşan tülbent, selüloz esaslı filtre kâğıtlarına yüksek oranda lamine edilebilmektedir. Polifenilen sülfitten yapılan monofilamentler dokunarak aşınmaya dirençli filtre kumaşı ve yüksek sıcaklığa dayanıklı taşıma bantları yapılmaktadır. Bu yüksek performanslı materyaller çok yüksek mekanik özelliklere dayanıklıdır. Yüksek ısı direnci sebebiyle PPS filamentlerden yapılan konveyör bantları yüksek hızlarda çalışabilir ve kurutma süresini kısaltmaktadır.
SONUÇ
20.yüzyılda otomotiv endüstrisinde güvenliğin ve konforun ön plana çıkmasıyla birlikte araçlarda tekstil materyallerinin kullanımı artmıştır. Yıllık yaklaşık 70 milyon aracın üretildiği dünyada, yaşam standartlarının artması ve insanların araç içerisinde çok daha fazla zaman geçirmesiyle birlikte, insanların araçtan beklentileri de daha üst seviyeye çıkmıştır. Bir aracın motoru ve kaportası kadar görünür yerlerde kullanılan koltuk kumaşı, halı gibi ürünlerin kalitesine eskiye kıyasla çok daha fazla önem verilmektedir. Koltuk üzerindeki döşemelik kumaşı eskiyen aşınan bir aracın, motorunun da yıprandığı düşünülmekte ve aracın değeri düşmektedir. Bunun sonucunda araç üreticileri rekabet edebilmek için kaporta ve motoru kadar tekstil malzemelerinin kalite standartlarını artırmıştır. Petrolün tükenmesi ve fiyatlarının artması araç üreticilerini, daha hafif malzeme kullanımına sevk etmektir. Bu bağlamda, metal parçalar karbon, cam, kevlar ve aramid gibi lif takviyeli kompozit ürünlerle yer değiştirmeye başlamıştır. Dokuma ve çok eksenli iplik yatırma (multiaxial) yöntemleriyle üretilen malzemeler RTM kompozit teknolojisiyle matris (yapıştırıcı) malzemeyle kompozit haline getirilmektedir. 1966 yılında seri üretimine başlanan ve 1980’li yılların başında üretimine son verilen kaportası cam elyaf ve poliester reçine olan Anadol aracına doğru bir geri dönüş olduğu açıktır. Güvenlik kurallarının artması neticesinde, aracın içinde seyahat edenleri ve aracın çarptığı kişileri korumak için, aracın içinde ve dışında açılacak hava yastıkları hava yastığının kullanımının artacağına işarettir.
Ekolojik kurallar ve reformlar, araçlarda geri kazanılmış tekstil malzemelerinin kullanımını artıracaktır. Özellikle %60-65 verimle pet şişelerden elde edilen poliester esaslı iğnelenmiş dokunmamış kumaşlar otomotiv endüstrisinde
halı olarak kullanılmaktadır. Ayrıca konforun önemli olduğu günümüzde motor sesini azaltan hacimli dokunmamış kumaşlara da ihtiyaç duyulacaktır. Otomotiv endüstrisinde halı olarak kullanılabilecek, kenevir, jüt, kendir, muz lifi gibi biyolojik bozunabilir bitkisel liflerden iğneleme teknolojisiyle dokunmamış kumaş üretimi diğer bir önemli konu olacaktır.